Fundamental Researches of Fluid and Combustion for the Hypersonic Flight
JAXA Supercomputer System Annual Report April 2018-March 2019
Report Number: R18ECMP18
Subject Category: Competitive Funding
- Responsible Representative: Kouichi Okita, Director, Research Unit IV, Research and Development Directorate
- Contact Information: Masahiro Takahashi(takahashi.masahiro@jaxa.jp)
- Members: Masahiro Takahashi, Masatoshi Kodera, Toshihiko Munakata, Masaaki Fukui, Masaharu Takahashi, Susumu Hasegawa, Sadatake Tomioka
Abstract
The wind tunnel tests by using sub-scaled models play important roles for the development of the air-breathing propulsion system for a hypersonic transporter. However, in some cases, the flow of the wind tunnel is ”vitiated” due to the heating process and/or the complex flow-path of the facility. To rise the total temperature to produce the high Mach number flow, a combustion heating is usually applied, introducing the water vaper to the air stream. The complex flow-path of the facility would increase turbulence. Both the phenomena might affect the supersonic combustion process. To clarify the effects of the flow vitiation and ultimately, to establish the adjustment methodology that can deduce the data of real flight from the wind tunnel data, JAXA has initiated the 5-years study. The final goal is conducting the flight experiment to obtain the data on the supersonic combustion in an actual flight condition and verify the methodology.
Reference URL
N/A
Reasons for using JSS2
Recently, hydrocarbon fuels become more promising fuels for a supersonic combustor than hydrogen because of those high thrust density. A gaseous ethylene is selected as the fuel for the present flight experiment. Ethylene is rather simple hydrocarbon, but much more chemical species contributes to the combustion process than hydrogen. In addition, the flow conditions in the supersonic combustor and those around the hypersonic flight test vehicle are quire severe. As a result, the CFD for the present design evaluation requires large computation time. Furthermore, many cases of the CFD must be executed for aerodynamic design of the flight test vehicle and the combustor model within the scheduled period. Therefore, the use of the JSS2 system is essential for the success of the present research program.
Achievements of the Year
To establish the design philosophy for the internal flow-path configuration of the supersonic combustor model for the present flight experiment, 3D CFD was conducted. Since the ethylene/air combustion model should have capability to reproduce the difference of the combustion process due to the difference of the gas composition of the engine incoming flow between the wind tunnel and the flight tests, a skeletal mechanism, which consists of 31 chemical species, was applied for the present CFD. The design requirement is to enhance the influence of the difference in the chemical composition of the engine incoming flows on combustion, which is large enough to be identified by the wall pressure measurement. It was considered that the higher the combustor pressure is, the larger difference between the combustor pressure of the wind tunnel test and that of the flight test would be obtained. From the CFD parametric study, the flow-path configuration, which is expected to achieve the supersonic-combustion-mode operation with the higher equivalence ratio and the higher combustion efficiency than the initial configuration, was obtained. The results also showed that the composition of the combustion gas would differ between the wind tunnel condition and the flight condition due to the introduction of the water vaper in the tunnel flow by the combustion heating.
3D CFD was also conducted to predict the aerodynamic characteristics of the flight test vehicle and to examine the effectiveness of the body shape modification to the improvement of the aerodynamic characteristics. The predicted surface pressure distributions on the nose section were also used for the design and development of a flush air-data sensing system (FADS) for the flight test vehicle. The preliminary wind tunnel tests of the FADS installed on a sub-scaled model have been conducted.
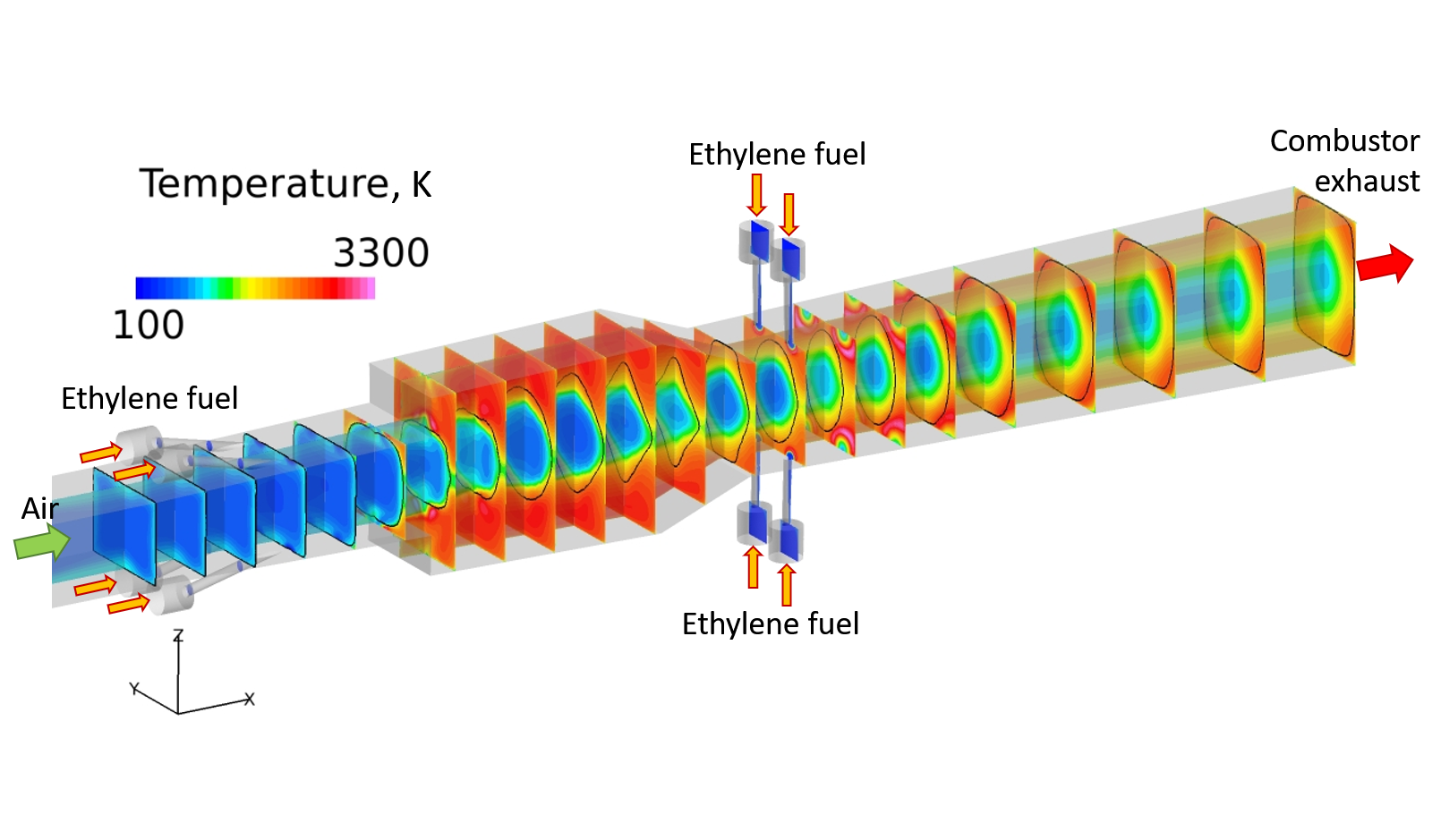
Fig.1: Numerical result of the static temperature distribution in the modified supersonic combustor; Flow conditions correspond to those for the flight Mach number of 6.1, the fuel is gaseous ethylene, the fuel equivalence ratio for the 1st and 2nd injectors are 0.25 and 0.25, the black line in each plane shows the sonic line.
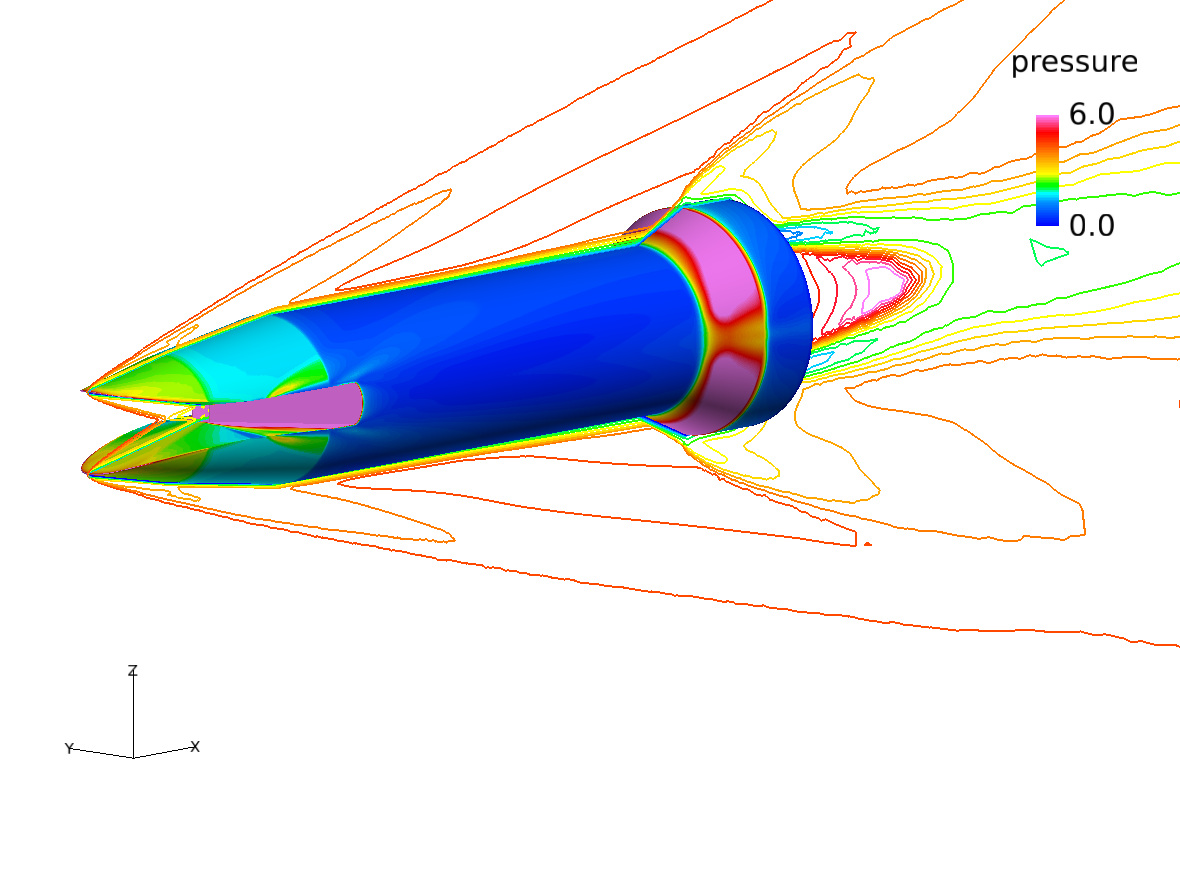
Fig.2: The predicted surface pressure distribution and the Mach number contours on the symmetric plane in the span-wise direction of the flight test vehicle; The flight Mach number of 6, the angle of attack of 0 degree.
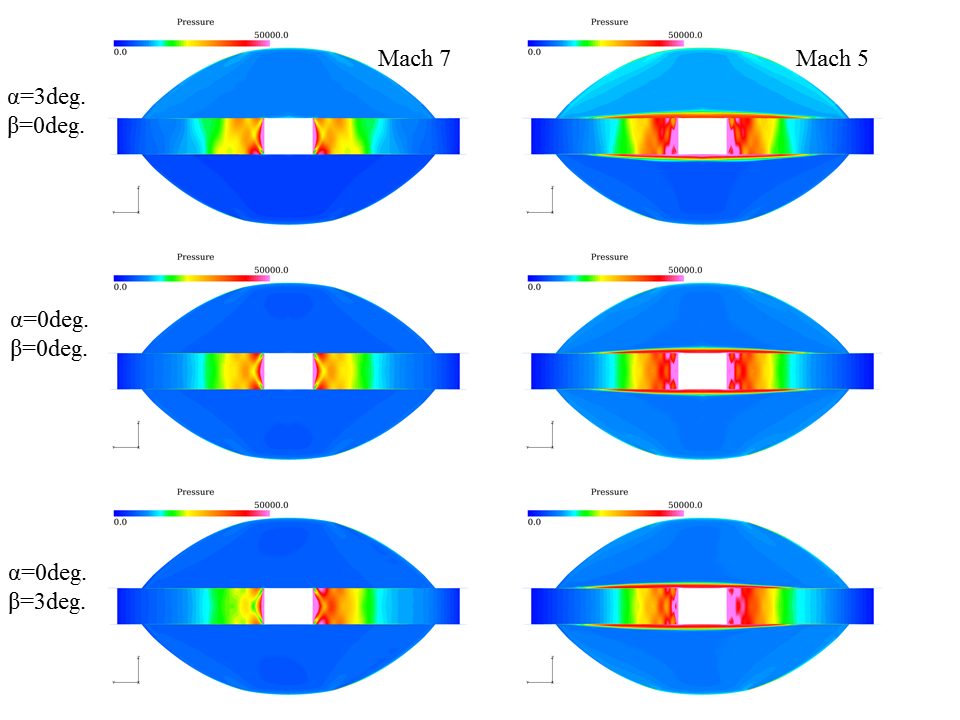
Fig.3: The surface pressure distributions on the inlet compression ramps and inlet sidewall of the flight test vehicle, which were used for the design of the flush air-data sensing system (FADS); The left and right figures in each row show the results of the flight Mach number of 7 and those of 5, the top figure shows that for α of 3 degree and β of 0 degree, the middle shows for α of 0 degree and β of 0 degree, the bottom shows for α of 0 degree and β of 3 degree. α is the angle of attack and β is the side slip angle.
Publications
– Non peer-reviewed papers
1) M. Takahashi, S. Tomioka, M. Kodera, K. Kobayashi, S. Hasegawa, T. Shimizu, J. Aono, T. Munakata, ”Combustor Flow-Path Design for a Scramjet Flight Experiment,” Proceedings of the 59th Conference on Aerospace Propulsion, JSASS-2019-0053, 2019.
2) H. Takahashi, K. Takasaki, K. Tani, M. Kodera, ”Design and Evaluation of A Hypersonic Flush Air-Data Sensing System for Sharp-Nosed Vehicles,” Proceedings of the 59th Conference on Aerospace Propulsion, JSASS-2019-0055, 2019.
– Oral Presentations
1) M. Takahashi, S. Tomioka, M. Kodera, K. Kobayashi, S. Hasegawa, T. Shimizu, J. Aono, T. Munakata, ”Combustor Flow-Path Design for a Scramjet Flight Experiment,” The 59th Conference on Aerospace Propulsion, 2A11, 2019.
2) H. Takahashi, K. Takasaki, K. Tani, M. Kodera, ”Design and Evaluation of A Hypersonic Flush Air-Data Sensing System for Sharp-Nosed Vehicles,” The 59th Conference on Aerospace Propulsion, 2A13, 2019.
Usage of JSS2
Computational Information
- Process Parallelization Methods: MPI
- Thread Parallelization Methods: N/A
- Number of Processes: 640 – 1280
- Elapsed Time per Case: 400 Hour(s)
Resources Used
Fraction of Usage in Total Resources*1(%): 0.45
Details
Please refer to System Configuration of JSS2 for the system configuration and major specifications of JSS2.
System Name | Amount of Core Time(core x hours) | Fraction of Usage*2(%) |
---|---|---|
SORA-MA | 4,227,867.20 | 0.52 |
SORA-PP | 1,801.84 | 0.01 |
SORA-LM | 0.00 | 0.00 |
SORA-TPP | 0.00 | 0.00 |
File System Name | Storage Assigned(GiB) | Fraction of Usage*2(%) |
---|---|---|
/home | 124.74 | 0.13 |
/data | 6,557.72 | 0.12 |
/ltmp | 2,718.10 | 0.23 |
Archiver Name | Storage Used(TiB) | Fraction of Usage*2(%) |
---|---|---|
J-SPACE | 1.90 | 0.07 |
*1: Fraction of Usage in Total Resources: Weighted average of three resource types (Computing, File System, and Archiver).
*2: Fraction of Usage:Percentage of usage relative to each resource used in one year.
JAXA Supercomputer System Annual Report April 2018-March 2019