Fundamental Researches of Fluid and Combustion for the Hypersonic Flight
JAXA Supercomputer System Annual Report February 2023-January 2024
Report Number: R23ECMP18
Subject Category: Competitive Funding
- Responsible Representative: Kouichi Okita, Director, Research Unit IV, Research and Development Directorate
- Contact Information: Masahiro Takahashi(takahashi.masahiro@jaxa.jp)
- Members: Masaaki Fukui, Susumu Hasegawa, Taku Inoue, Masatoshi Kodera, Masaharu Takahashi, Sadatake Tomioka, Masahiro Takahashi, Shun Takahashi, Gouji Yamada
Abstract
The wind tunnel tests by using sub-scaled models play important roles for the development of the air-breathing propulsion system for a hypersonic transporter. However, in some cases, the flow of the wind tunnel is ”vitiated” due to the heating process and/or the complicated flow-path of the facility. To raise the total temperature to match the conditon of high Mach number flow, a combustion heating is usually applied, introducing the water vaper to the air stream. The complicated flow-path of the facility would enhance turbulence. Both the phenomena might affect the supersonic combustion process. To clarify the effects of the flow vitiation and ultimately, to establish the adjustment methodology that can deduce the data of real flight from the wind tunnel data, JAXA has initiated the 5-years study. On July 24, 2022, S-520-RD1 rocket was launched from JAXA Uchinoura Space Center and successfully conducted a flight test to acquire supersonic combustion data in actual flight. In addition, a ground combustion test was conducted in the facility flow conditions that simulated those of the flight experiment, and wind tunnel test data approximating the actual flight data was acquired. We also confirmed that the CFD tool, whose model parameters were adjusted based on the ground test data, could predict the actual flight data within the target accuracy, and demonstrated the method for applying the ground test data to actual engine design.
Reference URL
Please refer to https://www.kenkai.jaxa.jp/research/pastres/supersonic.html .
Reasons and benefits of using JAXA Supercomputer System
Recently, hydrocarbon fuels become more promising fuels for a supersonic combustor than hydrogen because of those high thrust density. A gaseous ethylene is selected as the fuel for the present flight experiment. Ethylene is rather simple hydrocarbon, but much more chemical species contributes to the combustion process than hydrogen. In addition, the flow conditions in the supersonic combustor and those around the hypersonic flight test vehicle are quire severe. As a result, the CFD for the present design evaluation requires large computation time. Furthermore, many cases of the CFD must be executed for aerodynamic design of the flight test vehicle and the combustor model within the scheduled period. Therefore, the use of the JSS system is essential for the success of the present research program.
Achievements of the Year
This year, we continued the detailed analysis of the test results of the RD1 supersonic combustion flight experiment (conducted on July 24, 2022) and the post-flight ground test, and the development and verification of a tool for predicting supersonic combustor performance / hypersonic aerodynamic heating. We achieved the following results.
(1) Development and varidation of CFD based prediction tool for supersonic combustor performance
As for the CFD prediction tool for combustor performance, which was constructed in the RD-1 project, CFD analysis corresponding to the combustor test at RJTF after the flight test was conducted to investigate the grid dependency on the CFD results and compare them to the gas sampling data at the combustor exit. As a result, the CFD results showed that the grid dependency was relatively large, and the agreement with the gas sampling data was insufficient compared to that with the wall pressure data. (Fig. 1)
(2) Development of low-computational-cost prediction tool for surface heat flux of hypersonic flight vehicle
The surface heat fluxes obtained from flight experiments were predicted using several techniques, including the Euler CFD coupled with the reference temperature method and RANS CFD, to calculate the surface heat fluxes in hypersonic flow more efficiently. The results showed that RANS CFD predicted the experimental values well overall, but the combined Euler CFD and reference temperature method had difficulty predicting heat flux, mainly in regions with irregular surface texture. (Fig. 2)
(3) Improvement of accuracy of dynamic pressure measurement using Air Data Sensor
In the RD1 flight test, the Air Data Sensor (ADS) was installed to monitor changes in dynamic pressure during flight. When it exceeded a preset value, the fuel supply sequence was activated to start the supersonic combustion experiment. In the RD1 flight test, based on the CFD results of the flow around the nose section of the experiment vehicle, the ADS pressure sensors used for dynamic pressure estimation and the weight of each sensor output were determined, and a simple weighted linear summation of the ADS pressure sensor outputs estimated dynamic pressure. This year, the estimation method was re-examined to improve dynamic pressure estimation accuracy further. First, we applied linear multiple regression analysis, a statistical technique that predicts the dependent variable using multiple independent variables. Statistical machine learning methods (Gradient Boost, Cat Boost, Xgboost) were also introduced to improve the accuracy of the estimation further, and a significant improvement in accuracy was achieved. (Fig. 3)
(4) Post-flight data analysys of the heat flux data measured in the RD1 flight experiment
Surface heat fluxes of the RD1 flight experiment vehicle were measured by heat flux meters at an average flight Mach number of around 5.7 in the descent phase of its parabolic trajectory. Three thermocouples were installed in the heat fluxmeter at 1mm, 6mm,11mm in depth. The surface heat flux was estimated using ABAQUS from the temperature history at these three points.
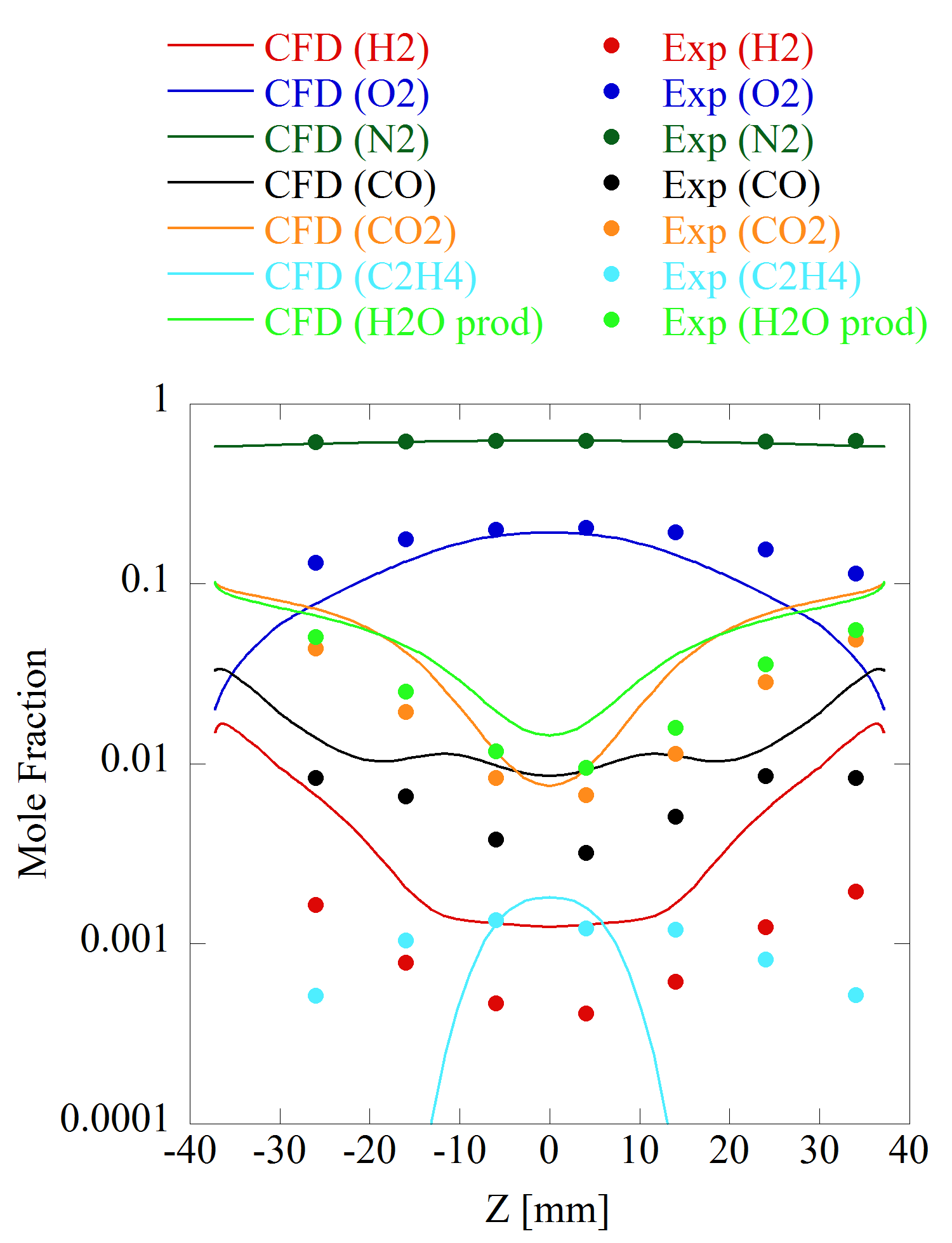
Fig.1: Comparison between CFD results and RJTF test data (mole fraction distributions for each species along combustor exit centerline)

Fig.2: The predicted heat flux distribution around the sensors installed on the flight experiment vehicle (marked with circle in the figure) at 200 kPa dynamic pressure is shown. The left and right figures show the surface heat flux distributions inside and outside the inlet of the flight experiment vehicle, respectively. In each figure, the upper half shows the results of the Euler simulation using a Cartesian grid with post-processing by the reference temperature method, and the lower half shows the results of the RANS simulation using an unstructured grid.
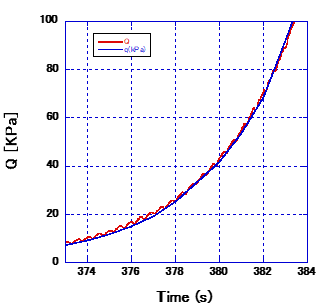
Fig.3: Comparison of dynamic pressure values predicted by using linear multiple regression analysis based on ADS pressure sensor outputs (red line) and dynamic pressure values deduced from radar tracking data of the flight experiment vehicle (blue line).
Publications
– Peer-reviewed papers
Takahashi, H., Hasegawa, S., Tani, K., “Simplified Real-Time Flush Air-Data Sensing System for Sharp-Nosed Hypersonic Vehicles,” Journal of Spacecraft and Rockets, September 2023. https://doi.org/10.2514/1.A35634
– Non peer-reviewed papers
1) Kodera, M., Takahashi, M., Kobayashi, K., and Tomioka, S., “CFD Prediction of Scramjet Combustor Performance for Flight Experiment of S-520-RD1,” Proceedings of the 55th Fluid Dynamics Conference/the 41st Aerospace Numerical Simulation Symposium, JSASS-2023-2071-A, 2023.
2) Kodera, M., Takahashi, M., Kobayashi, K., and Tomioka, S., “Construction and Validation of a CFD Prediction Tool of Scramjet Combustor Performance for a Flight Experiment,” AIAA Paper 2024-1192, 2024.
3) Takahashi, S., Yamada, G., Kodera, M., “Heat Flux Prediction around Complex Geometry Using Immersed Boundary Method in Hypersonic Flow,” Proceedings of the 55th Fluid Dynamics Conference/the 41st Aerospace Numerical Simulation Symposium, 2B13 (JAXA-SP-23-009), 2023.
4) Takahashi, S., Yamada, G., Takegoshi, M., Tani, K., “Coupled analysis of fluid and solid heat transfer by the Cartesian grid method,” Proceedings of the 37th Computational Fluid Dynamics Symposium (domestic), 1406-10-05, 2023.
5) Takahashi, S., Yamada, G., Kodera, M., Takegoshi, M., “Prediction of surface heat flux in hypersonic flow based on immersed boundary method and reference Temperature method,” AIAA Paper 2024-0647.
6) Tani, K., Takasaki, T., Hasegawa, S., “The Analysis of Flight Trajectory of S-520-RD1,” Proceedings of the 34th ISTS, 2023-m-01, 2023.
7) Tani, K., Hasegawa, S., “Numerical Simulations Applied to the Development of S-520-RD1,” Proceedings of the 55th Fluid Dynamics Conference/the 41st Aerospace Numerical Simulation Symposium, 2B10, 2023.
8) Hasegawa, S., Tani, K., “Aerodynamic Topics in Hypersonic Flight Tests,” Proceedings of the 55th Fluid Dynamics Conference/the 41st Aerospace Numerical Simulation Symposium, 2B11, 2023.
9) Hasegawa, S., Tani, K., “Evaluation of Air Data Sensor and Statistical Analysis of Dynamic Pressure in Hypersonic Flight Experiment,” Proceedings of the 36th Computational Mechanics Conference (CMD2023), GS-0008, 2023.
10) Hasegawa, S., Tani, K., “Evaluation of Air Data Sensors and Statistical Analysis of the Dynamic Pressure of Hypersonic Flight Experiments,” AIAA Paper 2024-2681, 2024.
11) Takegoshi, M., “Thermal, Structural and Vibration Analysis on the design of S-520-RD1 Flight Experiment Vehicle,” Proceedings of the 55th Fluid Dynamics Conference/the 41st Aerospace Numerical Simulation Symposium, 2B14, 2023.
12) Takegoshi, M., Takahashi, S., Yamada, G., Tani, K., ”Differences in aerodynamic heating measurement results between S-520-RD1 flight experiment and RJTF wind tunnel experiment,” R5 Space Transportation Symposium, STCP-2023-033, 2024.
– Oral Presentations
1) Kodera, M., Takahashi, M., Kobayashi, K., and Tomioka, S., “CFD Prediction of Scramjet Combustor Performance for Flight Experiment of S-520-RD1,” The 55th Fluid Dynamics Conference/the 41st Aerospace Numerical Simulation Symposium, 2023.
2) Kodera, M., Takahashi, M., Kobayashi, K., and Tomioka, S., “Construction and Validation of a CFD Prediction Tool of Scramjet Combustor Performance for a Flight Experiment,” AIAA SciTech 2024 Forum and Exposition, 2024.
3) Takahashi, S., Yamada, G., Kodera, M., “Heat Flux Prediction around Complex Geometry Using Immersed Boundary Method in Hypersonic Flow,” The 55th Fluid Dynamics Conference/the 41st Aerospace Numerical Simulation Symposium, 2023.
4) Takahashi, S., Yamada, G., Takegoshi, M., Tani, K., “Coupled analysis of fluid and solid heat transfer by the Cartesian grid method,” The 37th Computational Fluid Dynamics Symposium (domestic), , 2023.
5) Takahashi, S., Yamada, G., Kodera, M., Takegoshi, M., “Prediction of surface heat flux in hypersonic flow based on immersed boundary method and reference Temperature method,” AIAA SciTech 2024, 2024.
6) Takahashi, S., Yamada, G., Kodera., M, Takegoshi, M., Tani, K., “Heat flux prediction for hypersonic flight tests with air-breathing engines,” R5 Space Transportation Symposium, 2024.
7) Tani, K., Takasaki, T., Hasegawa, S., “The Analysis of Flight Trajectory of S-520-RD1,” The 34th ISTS, 2023.
8) Tani, K., Hasegawa, S., “Numerical Simulations Applied to the Development of S-520-RD1,” The 55th Fluid Dynamics Conference/the 41st Aerospace Numerical Simulation Symposium, 2023.
9) Hasegawa, S., Tani, K., “Aerodynamic Topics in Hypersonic Flight Tests,” The 55th Fluid Dynamics Conference/the 41st Aerospace Numerical Simulation Symposium, 2023.
10) Hasegawa, S., Tani, K., “Evaluation of Air Data Sensor and Statistical Analysis of Dynamic Pressure in Hypersonic Flight Experiment,” The 36th Computational Mechanics Conference (CMD2023), 2023.
11) Hasegawa, S., Tani, K., “Evaluation of Air Data Sensors and Statistical Analysis of the Dynamic Pressure of Hypersonic Flight Experiments,” AIAA SciTech 2024 Forum and Exposition, 2024.
12) Takegoshi, M., Kodera, M., Hasegawa, S., Yoshida, M., Tani, K., Taguchi, H., Tomioka, S., Takahashi, M., Momose, M., “Thermal, Structural and Vibration Analysis on the design of S-520-RD1 Flight Experiment Vehicle,” The 55th Fluid Dynamics Conference/the 41st Aerospace Numerical Simulation Symposium, 2023.
13) Takegoshi, M., Takahashi, S., Yamada, G., Tani, K., ”Differences in aerodynamic heating measurement results between S-520-RD1 flight experiment and RJTF wind tunnel experiment,” R5 Space Transportation Symposium, 2024.
Usage of JSS
Computational Information
- Process Parallelization Methods: MPI
- Thread Parallelization Methods: OpenMP/Automatic Parallelization
- Number of Processes: 960 – 2000
- Elapsed Time per Case: 120 Hour(s)
JSS3 Resources Used
Fraction of Usage in Total Resources*1(%): 2.02
Details
Please refer to System Configuration of JSS3 for the system configuration and major specifications of JSS3.
System Name | CPU Resources Used(Core x Hours) | Fraction of Usage*2(%) |
---|---|---|
TOKI-SORA | 54335930.63 | 2.45 |
TOKI-ST | 57971.89 | 0.06 |
TOKI-GP | 0.00 | 0.00 |
TOKI-XM | 0.00 | 0.00 |
TOKI-LM | 2592.02 | 0.20 |
TOKI-TST | 0.00 | 0.00 |
TOKI-TGP | 0.00 | 0.00 |
TOKI-TLM | 0.00 | 0.00 |
File System Name | Storage Assigned(GiB) | Fraction of Usage*2(%) |
---|---|---|
/home | 699.52 | 0.58 |
/data and /data2 | 48938.50 | 0.30 |
/ssd | 5135.50 | 0.49 |
Archiver Name | Storage Used(TiB) | Fraction of Usage*2(%) |
---|---|---|
J-SPACE | 10.12 | 0.04 |
*1: Fraction of Usage in Total Resources: Weighted average of three resource types (Computing, File System, and Archiver).
*2: Fraction of Usage:Percentage of usage relative to each resource used in one year.
ISV Software Licenses Used
ISV Software Licenses Used(Hours) | Fraction of Usage*2(%) | |
---|---|---|
ISV Software Licenses(Total) | 2808.91 | 1.27 |
*2: Fraction of Usage:Percentage of usage relative to each resource used in one year.
JAXA Supercomputer System Annual Report February 2023-January 2024