Environment Conscious Aircraft Systems Research in Eco-wing Technology
JAXA Supercomputer System Annual Report April 2016-March 2017
Report Number: R16E0107
- Responsible Representative: Yoshikazu Makino(Next Generation Aeronautical Innovation Hub Center, Aeronautical Technology Directorate)
- Contact Information: Dongyoun Kwak(kwak.dongyoun@jaxa.jp)
- Members: Yuki Oda, Yuta Suzuki, Hotaka Kobayashi, Shun Goto, Tsubasa Kimura, Dongyoun Kwak, Kaoruko Etou, Yusuke Kondo, Takashi Yamazaki, Shihoko Endo
- Subject Category: Aviation(Aircraft,Body sound)
Abstract
Innovative drag reduction technologies are investigated to reduce the fuel consumption for a conventional aircraft configuration. Aircraft noise prediction technologies and the conceptual design technologies are also developed for future aircraft which achieve low noise and high efficiency.
Goal
Please refer ‘Eco-wing technology | ECAT – Environment-Conscious Aircraft Technology Program | Aeronautical Technology Directorate‘.
Objective
Please refer ‘Eco-wing technology | ECAT – Environment-Conscious Aircraft Technology Program | Aeronautical Technology Directorate‘.
References and Links
Please refer ‘Eco-wing technology | ECAT – Environment-Conscious Aircraft Technology Program | Aeronautical Technology Directorate‘.
Use of the Supercomputer
CFD analysis are used for the understanding of aerodynamic characteristics and evaluation of the performance in the aircraft design phase.
Necessity of the Supercomputer
Huge calculation resources and costs were required for the high fidelity and quick response CFD analysis for the optimum aerodynamic design and aeroacoustic simulation process on complex aircraft geometry. JSS2 can achieve those requirements, the cost and time are drastically saved on the CFD analysis.
Achievements of the Year
Drag reduction technologies and noise reduction technologies are investigated by cooperation with universities.
On the drag reduction technologies, two wingtip geometries were designed to reduce induced drag component using numerical analysis. A split tip winglet configuration was examined by using numerical approaches. The split tip winglet configuration was defined by using thirteen design variables, and then its geometry was optimized to minimize aerodynamic drag force. As a result, the reduction of the induced drag strength and of strong vortex areas can be observed with the optimal split tip winglet. The weights of wing structure and of fuel were also estimated. The wing structural weight is increased while the fuel weight is reduced in the optimal design. (Fig.1). A downward or upward pointing rakelet, which is a wingtip configuration with a raked wingtip accompanied by a downward or upward pointing winglet section, in mainly considered. The upward and downward pointing rakelets with a 105% span length achieve a drag reduction more than 10 counts compared with the baseline configuration(Fig.2). Structural weight estimations were also conducted. The downward pointing rakelet indicates the largest decrease in total weight.
On the aircraft noise reduction technologies, a slat noise was understood by aeroacoustic simulations. Relationship between the slat noise level and the size of flow separation (distance between the slat trailing-edge and re-attachment point of shear layer on the lower surface of the slat cove) was evaluated by higher-order unsteady aeroacoustic simulations(Fig.3). The results validated a simplified objective function to represent noise reduction for noise/aerodynamic slat-setting design optimization using low-cost steady RANS simulations.
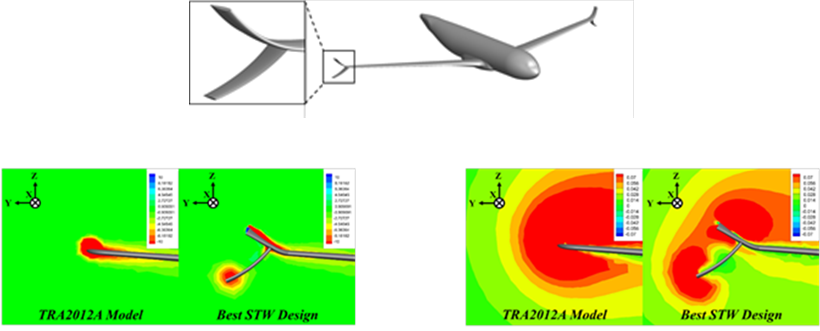
Fig.1:(top) TRA2012A wing-body configuration with STW, (left) Vorticity distributions of representative designs, (right) Induced drag source distributions of representative designs
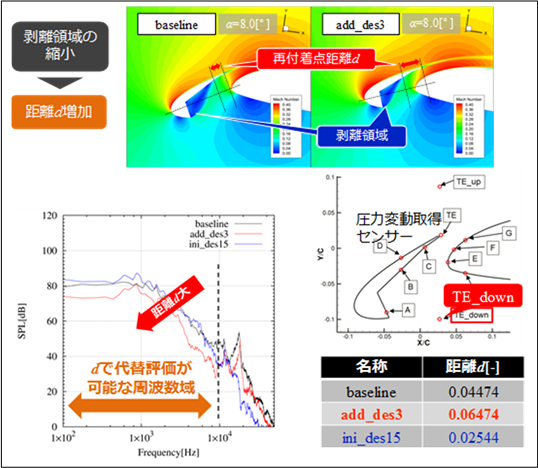
Fig. 3:Relationship between the slat noise level and the size of flow separation (distance between the slat trailing-edge and re-attachment point of shear layer on the lower surface of the slat cove)
Publications
Presentations
1) Oda, Y., Yuhara, T. and Rinoie, K., Studies on Wingtip Geometries by Optimum span wise Lift Distribution Design Method, The 55th AIAA Aerospace Sciences Meeting, 2017.
Computational Information
- Parallelization Methods: Process Parallelization,Thread Parallelization,Hybrid Parallelization
- Process Parallelization Methods: MPI
- Thread Parallelization Methods: OpenMP ,Automatic Parallelization
- Number of Processes: 15-50
- Number of Threads per Process: 4-32
- Number of Nodes Used: 1-32
- Elapsed Time per Case (Hours): 0.5-300
- Number of Cases: 300
Resources Used
Total Amount of Virtual Cost(Yen): 16,886,769
Breakdown List by Resources
System Name | Amount of Core Time(core x hours) | Virtual Cost(Yen) |
---|---|---|
SORA-MA | 9,582,029.96 | 15,608,195 |
SORA-PP | 68,695.42 | 586,521 |
SORA-LM | 0.19 | 4 |
SORA-TPP | 0.00 | 0 |
File System Name | Storage assigned(GiB) | Virtual Cost(Yen) |
---|---|---|
/home | 870.42 | 8,210 |
/data | 47,060.99 | 443,927 |
/ltmp | 16,927.09 | 159,673 |
Archiving System Name | Storage used(TiB) | Virtual Cost(Yen) |
---|---|---|
J-SPACE | 25.99 | 80,235 |
Note: Virtual Cost=amount of cost, using the unit price list of JAXA Facility Utilization program(2016)
JAXA Supercomputer System Annual Report April 2016-March 2017