A Study on High-order Accurate Fluid Dynamic Simulations for Rotating Fluid Machinery
JAXA Supercomputer System Annual Report April 2016-March 2017
Report Number: R16E0058
- Responsible Representative: Hikaru Aono(Tokyo University of Science)
- Contact Information: Hikaru Aono(aono@rs.tus.ac.jp)
- Members: Hikaru Aono
- Subject Category: Space(other )
Abstract
This project relates to the development of fluid analysis technology that can be applied to the design of rotating fluid element in turbo pump. In this fiscal year, large-eddy simulation analysis and its verification were carried out for a flow around a small axial flow fan with a low Reynolds number condition and available verification data. From the computed results, it was possible to demonstrate detailed unsteady fluid phenomena around the fan and quantitative evaluation of prediction accuracy. We are planning to proceed with verification using pumps and turbines in the near future.
Goal
Development of computational fluid dynamics that can be applied to the development and design of rotary fluid element devices (i.e. inducers, impellers, turbines, etc.) in turbo pumps for rocket engines represented by engines of LE-7A and reusable observation rockets.
Objective
In order to realize high-accurate fluid analysis of rotating fluid element devices (inducers, impellers, turbines, etc.) in a turbo pump, the development of robust grid generation method around a complicated shape, a highly accurate and high-resolution computational scheme, and appropriate moving boundary method are necessary. In this project, we have developed a fluid analysis program that was composed of a sixth order compact finite difference method and overlapping grid technique. The developed fluid analysis program was applied to the flow around the small fan in which the experiment data exists and its validity was confirmed.
References and Links
N/A
Use of the Supercomputer
Supercomputer was used to perform three-dimensional turbulent flow simulations around the small fan and debug the program developed. In addition, the fluid analysis program developed in this project has already been tuned to JSS2 and can fully utilize the performance of supercomputer.
Necessity of the Supercomputer
In order to analyze the quantitative flow field characteristics around the rotating fan with the Reynolds number of 105, it is necessary to use at least tens of thousands of computational grid points for the simulation and a long time of several tens of revolutions or more. Therefore, the calculation of this scale (number of grid points, calculation time) is possible only by using supercomputer. In addition, in order to directly calculate the aerodynamic acoustic field around the rotating fan, which is not addressed in this analysis, it is necessary to calculate for a long time using at least hundreds of millions of computational grid points. Furthermore, by using numerical simulation, there is also an advantage that it is possible to obtain characteristics of fluid force acting on impellers and boss of a fan that is hard to evaluate by experiments.
Achievements of the Year
The large-eddy simulation was performed under the operating condition at the maximum flow rate of the small fan (the Reynolds number based on the blade tip speed and diameter of the fan is about 105). Figure 1 showed the axial instantaneous velocity distribution around the fan after twenty-five rotations from the rest. The initial flow field around the fan was assumed to be quiescent. It was found that the flow in front of the fan was sucked in by the rotation of the fan and the unsteady flow was generated on the downstream side. Figure 2 visualized the flow around the fan with vorticity distribution at the same timing as Fig. 1. It was seen that the flow near the root and tip of the impeller were separated from the leading edge, formed the separated shear layer and vortices from it. Comparing the sound pressure level obtained by calculation at one meter ahead of the fan with the experimental data, the first blade passing frequency got nearly quantitative agreement. However, it was observed that a difference between the sound pressure level at the broadband frequency due to the turbulence and at higher blade passing frequencies. We expected that the cause was the presence or absence of the casing and the spatial grid resolution.
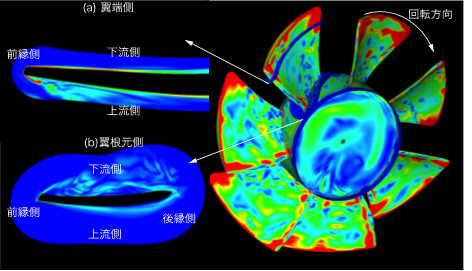
Fig.2:Snapshots of instantaneous vorticity contours around the small fan: selected impeller sections (left) and perspective view (right).
Publications
Presentations
1) Aono, Takahashi, Mamori, Fukushima, Fujii, Yamamoto, Murakami, A Numerical Study on Flow Features around Small Axial Fan using High-Resolution Computational Scheme, Inter-Noise 2017,submitted for presentation. (2017) [scheduled]
Computational Information
- Parallelization Methods: Hybrid Parallelization
- Process Parallelization Methods: MPI
- Thread Parallelization Methods: OpenMP,Automatic Parallelization
- Number of Processes: 32
- Number of Threads per Process: 2
- Number of Nodes Used: 50
- Elapsed Time per Case (Hours): 1000
- Number of Cases: 1
Resources Used
Total Amount of Virtual Cost(Yen): 459,960
Breakdown List by Resources
System Name | Amount of Core Time(core x hours) | Virtual Cost(Yen) |
---|---|---|
SORA-MA | 272,388.28 | 446,005 |
SORA-PP | 0.00 | 0 |
SORA-LM | 0.00 | 0 |
SORA-TPP | 0.00 | 0 |
File System Name | Storage assigned(GiB) | Virtual Cost(Yen) |
---|---|---|
/home | 19.07 | 105 |
/data | 1,953.13 | 10,798 |
/ltmp | 390.63 | 2,159 |
Archiving System Name | Storage used(TiB) | Virtual Cost(Yen) |
---|---|---|
J-SPACE | 0.49 | 891 |
Note: Virtual Cost=amount of cost, using the unit price list of JAXA Facility Utilization program(2016)
JAXA Supercomputer System Annual Report April 2016-March 2017