Investigation of internal flow of aircraft combustor for Green Engine Project
JAXA Supercomputer System Annual Report April 2016-March 2017
Report Number: R16E0004
- Responsible Representative: Toshiya Nakamura(Aeronautical Technology Directorate, Next Generation Aeronautical Innovation Hub Center)
- Contact Information: Mitsumasa Makida(makida@chofu.jaxa.jp)
- Members: Mitsumasa Makida, Naoki Nakamura
- Subject Category: Aviation(Aircraft engine)
Abstract
In the development process of aircraft combustors, air mass flow distribution between fuel nozzles, dilution and cooling air holes on the liner effects performances of combustors. So it is important to understand the internal flow and estimate the mass flow distribution. In this research, we conduct cold-flow simulations of internal flow inside the combustor which faithfully simulates the configuration of practical combustor. Then we aim to develop methods to analyze aerodynamic performance of combustors such as air mass flow distribution with high accuracy.
Goal
This research aims to develop a cold-flow simulation code which can estimate internal flow of aircraft combustor with high accuracy.
Objective
In this research, we conduct cold-flow simulations of internal flow inside the combustor which faithfully simulates the configuration of practical combustor. Then we aim to develop methods to analyze aerodynamic performance of combustors such as air mass flow distribution with high accuracy.
References and Links
Please refer ‘Green engine technology | ECAT – Environment-Conscious Aircraft Technology Program | Aeronautical Technology Directorate‘.
Use of the Supercomputer
It is important to do parametric case study with slightly different geometry, and each case needs large scale simulation. To conduct such simulation and visualization effectively, we use the supercomputer with high parallelization efficiency.
Necessity of the Supercomputer
It is important to do parametric case study with slightly different geometry, and each case needs large scale simulation. To conduct such simulation effectively, we need the super computer with high parallelization efficiency.
Achievements of the Year
In this fiscal year, we conducted cold-flow simulations for a multi-sector combustor which consisted of three single-sector two-stage premixed combustors. These simulations aimed to estimate the effect of side walls on the internal flow of the combustor. After this, we will conduct parametric case study with different combustor configurations aiming to select good configuration, and utilize the information for the development of combustors.
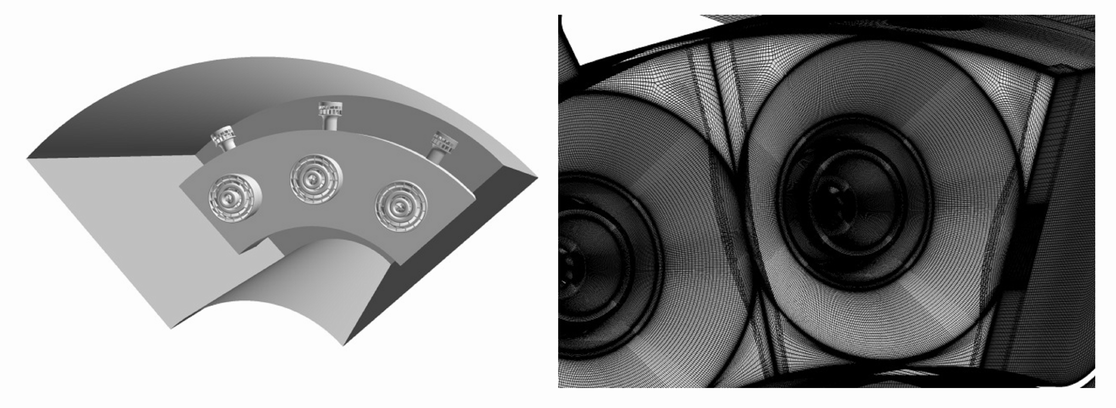
Fig.1:Configuration and calculation grids of combustor(Total configuration viewed from inlet(left), Calculation grids on downstream wall of fuel nozzles(right))
Publications
N/A
Computational Information
- Parallelization Methods: Hybrid Parallelization
- Process Parallelization Methods: MPI
- Thread Parallelization Methods: Automatic Parallelization
- Number of Processes: 128
- Number of Threads per Process: 4
- Number of Nodes Used: 16
- Elapsed Time per Case (Hours): 250
- Number of Cases: 1
Resources Used
Total Amount of Virtual Cost(Yen): 2,699,328
Breakdown List by Resources
System Name | Amount of Core Time(core x hours) | Virtual Cost(Yen) |
---|---|---|
SORA-MA | 1,616,700.82 | 2,654,742 |
SORA-PP | 2,667.14 | 22,772 |
SORA-LM | 0.00 | 0 |
SORA-TPP | 0.00 | 0 |
File System Name | Storage assigned(GiB) | Virtual Cost(Yen) |
---|---|---|
/home | 18.42 | 173 |
/data | 1,038.51 | 9,796 |
/ltmp | 1,255.58 | 11,843 |
Archiving System Name | Storage used(TiB) | Virtual Cost(Yen) |
---|---|---|
J-SPACE | 0.00 | 0 |
Note: Virtual Cost=amount of cost, using the unit price list of JAXA Facility Utilization program(2016)
JAXA Supercomputer System Annual Report April 2016-March 2017