aFJR Project
aFJR: Advanced Fan Jet Research *1)
Environmental standards for aircraft engines have become tightened amid global warming, and the world’s demand for more green engines with better fuel efficiency and low emissions is growing. JAXA is developing technologies to make lighter fans and low-pressure turbines with higher aerodynamic efficiency for increased engine bypass ratios *2), and will evaluate the effectiveness of such advanced technologies by demonstration experiments. JAXA also supports Japanese aero-engine manufacturers to reach a level of technology maturity sufficient to assume a role in the designing of next-generation engines for international projects.
*1) Joint research with IHI Corporation, the University of Tokyo, University of Tsukuba, Kanazawa Institute of Technology
*2) bypass ratios: the ratio of the amount of air flow through the fan only and that through the engine core
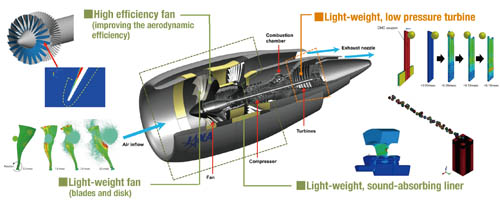
aFJR: Advanced Fan Jet Research
Impact Fracture Analysis of CMC LPT Blades
The impact fracture modeling method has been developed for the CMC Low Pressure Turbine (LPT) tangling design at an engine shaft failure event in
the JAXA/IHI aFJR project. Figure shows the analysis model of the cascades of
CMC low pressure turbine blades at the moment of contact with the cascade of stator vanes. It was found that the cascade of CMC rotor blades were fractured within the time specified.
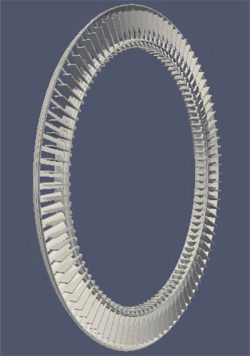
CMC LPT Blades
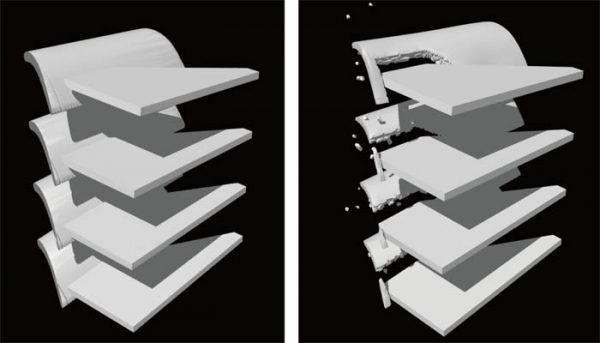
CMC LPT Rotor Blades and fractured Blades
High efficiency fan (improving the aerodynamic efficiency)
We introduce aerodynamic design technology for laminar flow fans by improving the shape of fan blades. The technology will move back the transition point from laminar flow to turbulence so that drag will be reduced.
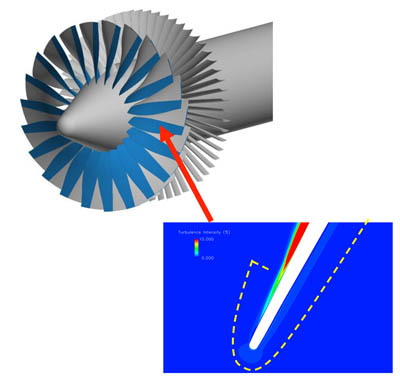
Transition simulation for fan rotor blades
Light-weight, low pressure turbine
We introduce a ceramic matrix composite (CMC) into low pressure turbine blades to reduce the weight, by developing a prediction method of impact fracture phenomenon to be applied to blade design.

High speed impact simulation of a CMC test piece
Light-weight fan (blades and disk)
We develop lightweight solutions with hollow CFRP fan blades. For the metal disk that holds the rotating fan blades, we create new metal processing techniques to realize weight reduction while maintaining strength.
Light-weight, sound-absorbing liner
The sound-absorbing liner is a honeycomb sandwich panel made of aluminum alloy, placed inside the engine cover to reduce noise. We reduce its weight by changing the material to resin without sacrificing sound-absorbing performance.
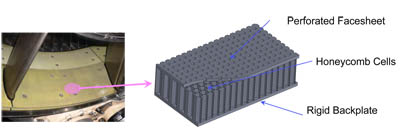
Sound-absorbing liner and its inner structure
More information about aFJR Project